STEEL SOLUTIONS
STEEL SOLUTIONS
We are experienced steel supplier and contractor in Malaysia who can provide many types and grades of steel for construction, manufacturing, architecture and building framework purposes. Steel Malaysia can be customarily prepared for bulk orders, measured thickness and length and shapes as suited to your project plannings. The choice of steel and its quality is critical to ensure the excellence of the end product and guarantees the satisfaction and safety of the end-user.
STAINLESS STEEL
Steel is a form of iron and carbon alloy while stainless steel is an upgraded form of low carbon steel, incorporating 10% of chromium or more. The addition of chromium is the key element as to why stainless steel is able to resist corrosion. Stainless steel also has a self-healing mechanism, in other words when scratched or damaged otherwise, a transparent layer will instantaneously reform under the influence of oxygen from atmospheric air. These properties can be further enhanced through the addition of foreign elements, such as nickel, molybdenum, titanium, niobium, nitrogen and manganese. Other reasons that make stainless steel such a versatile product in every industrial and commercial sector, is its resistance in a very broad temperature range, making them suitable for chemical, oil and gas industries that operate in highly demanding environments. Its exceptional mechanical strength also makes it very prominent in the construction, manufacturing and automotive industry. Stainless steel is easily welded, has an attractive finish and requires minimum maintenance, and is therefore used to manufacture many home appliances, particularly kitchen accessories and wall cabinets. Depending on its use and applications, stainless steel can come in a range of grades and specifications.
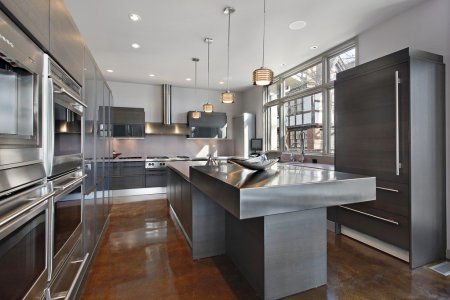
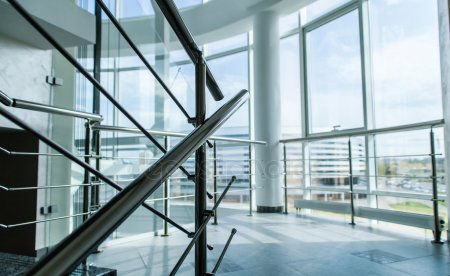


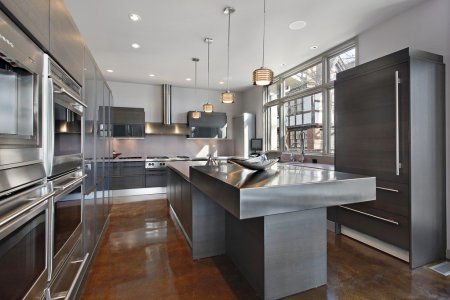
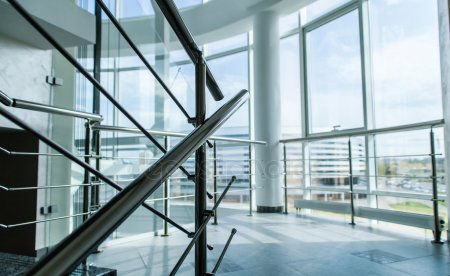


STAINLESS STEEL
Steel is a form of iron and carbon alloy while stainless steel is an upgraded form of low carbon steel, incorporating 10% of chromium or more. The addition of chromium is the key element as to why stainless steel is able to resist corrosion. Stainless steel also has a self-healing mechanism, in other words when scratched or damaged otherwise, a transparent layer will instantaneously reform under the influence of oxygen from atmospheric air. These properties can be further enhanced through the addition of foreign elements, such as nickel, molybdenum, titanium, niobium, nitrogen and manganese. Other reasons that make stainless steel such a versatile product in every industrial and commercial sector, is its resistance in a very broad temperature range, making them suitable for chemical, oil and gas industries that operate in highly demanding environments. Its exceptional mechanical strength also makes it very prominent in the construction, manufacturing and automotive industry. Stainless steel is easily welded, has an attractive finish and requires minimum maintenance, and is therefore used to manufacture many home appliances, particularly kitchen accessories and wall cabinets. Depending on its use and applications, stainless steel can come in a range of grades and specifications.
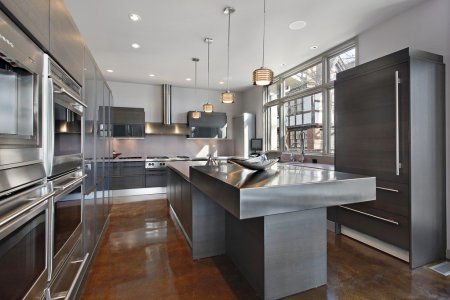
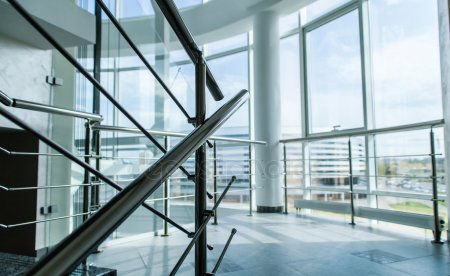


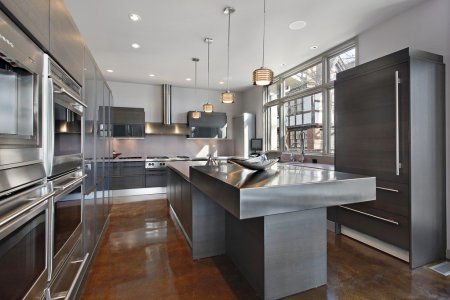
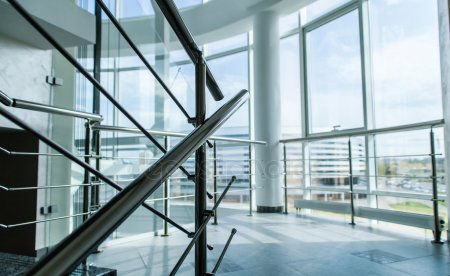




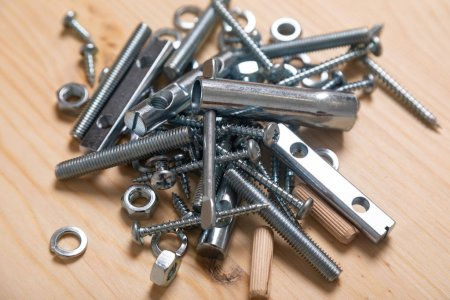





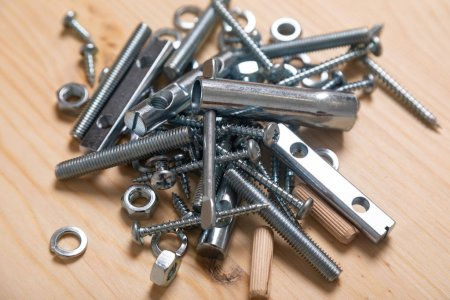



MILD STEEL
Mild steel is also known as “low-carbon steel” and as its name suggests, it can be considered a subcategory of carbon steel with a lower weight of carbon by a range of 0.05% to 0.25%. With less carbon content, mild steel is more ductile, machinable and weldable; however, this also means that it is near impossible to harden and strengthen it during heating and quenching. As there are a limited amount of foreign particles to block dislocations in its crystal lattice, mild steel is has a lower tensile strength than other types of high carbon and alloy steels. They are also magnetic due to its high amount of iron and ferrite. The lack of alloying properties, however, causes mild steel to be susceptible to oxidation and corrosion if unproperly coated. For economical and affordability reasons, mild steel is very versatile and readily available on the market in different forms, dimensions, shapes and grades, such as cold-rolled, annealed, sheets or strips. Their mechanical properties are especially ideal in the automotive industry to form body panels, plates and wire products owing to its malleability. Other applications include stampings, forgings, seamless tubes and boilerplates.


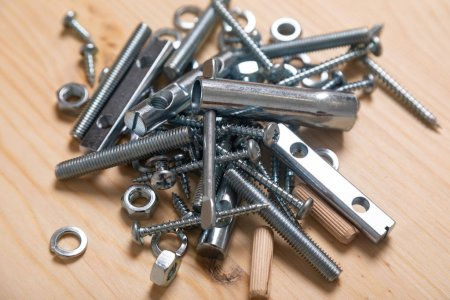





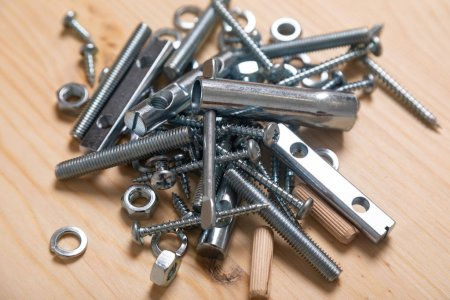



MILD STEEL
Mild steel is also known as “low-carbon steel” and as its name suggests, it can be considered a subcategory of carbon steel with a lower weight of carbon by a range of 0.05% to 0.25%. With less carbon content, mild steel is more ductile, machinable and weldable; however, this also means that it is near impossible to harden and strengthen it during heating and quenching. As there are a limited amount of foreign particles to block dislocations in its crystal lattice, mild steel is has a lower tensile strength than other types of high carbon and alloy steels. They are also magnetic due to its high amount of iron and ferrite. The lack of alloying properties, however, causes mild steel to be susceptible to oxidation and corrosion if unproperly coated. For economical and affordability reasons, mild steel is very versatile and readily available on the market in different forms, dimensions, shapes and grades, such as cold-rolled, annealed, sheets or strips. Their mechanical properties are especially ideal in the automotive industry to form body panels, plates and wire products owing to its malleability. Other applications include stampings, forgings, seamless tubes and boilerplates.
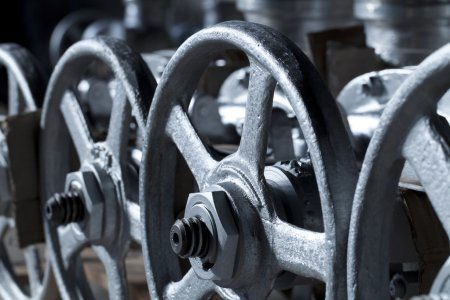







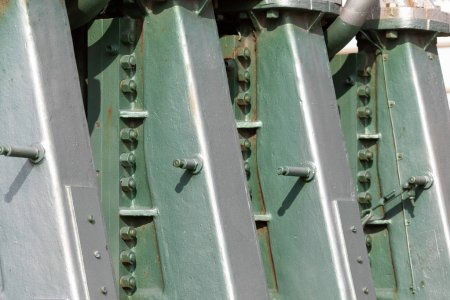
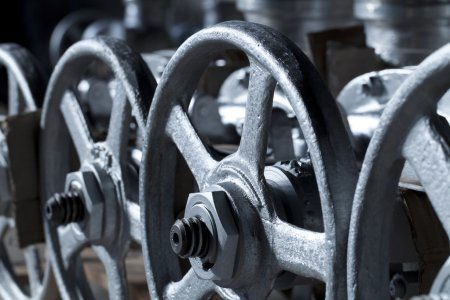







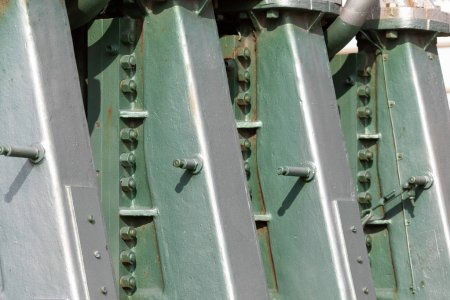
CARBON STEEL
Carbon steel is a relatively broad term for an alloy of iron and carbon and may be used in reference to steels that are not stainless steel. Carbon element is being introduced in the range of 0.12% to 2.0% as a hardening agent to prevent dislocations of a perfectly aligned iron crystal lattice. A higher carbon content increases the hardness and strength of the carbon steel through heat treatment, but on the flip side, it becomes less ductile and malleable. The variation of carbon steel grades is commonly determined by the carbon concentration in the steel from low, medium to high. Effectively, the carbon percentage influences the elasticity, ductility, tensile strength as well as the presence of ferrite, pearlite and cementite of the carbon steel. Unlike stainless steel, carbon steel is prone to rust and corrosion when exposed to moisture. Considering its strength and durability, carbon steel is extensively used in engineering and construction material in a large industrial scale. Ultra-high carbon steel, commonly known as “cast iron”, are typically used for extremely hard components such as blades, hot water radiators, industrial casting and lamp post.
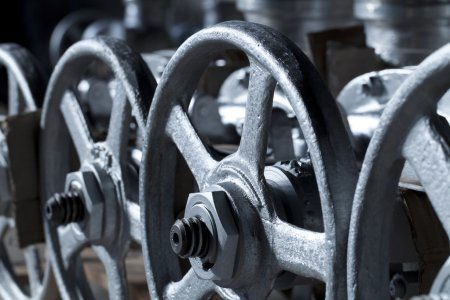







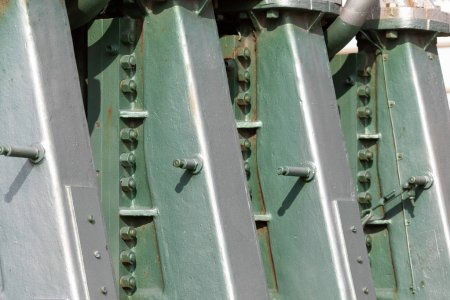
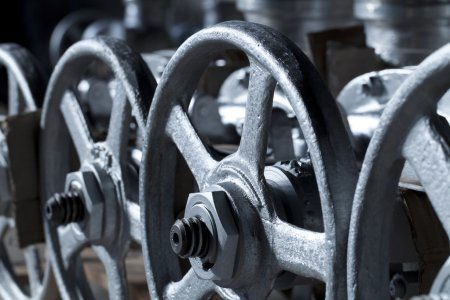







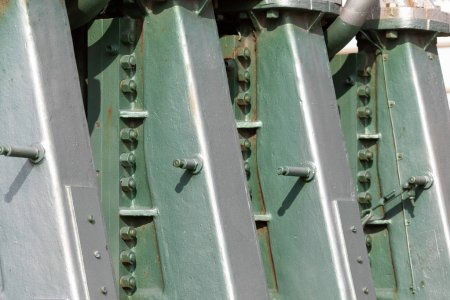
CARBON STEEL
Carbon steel is a relatively broad term for an alloy of iron and carbon and may be used in reference to steels that are not stainless steel. Carbon element is being introduced in the range of 0.12% to 2.0% as a hardening agent to prevent dislocations of a perfectly aligned iron crystal lattice. A higher carbon content increases the hardness and strength of the carbon steel through heat treatment, but on the flip side, it becomes less ductile and malleable. The variation of carbon steel grades is commonly determined by the carbon concentration in the steel from low, medium to high. Effectively, the carbon percentage influences the elasticity, ductility, tensile strength as well as the presence of ferrite, pearlite and cementite of the carbon steel. Unlike stainless steel, carbon steel is prone to rust and corrosion when exposed to moisture. Considering its strength and durability, carbon steel is extensively used in engineering and construction material in a large industrial scale. Ultra-high carbon steel, commonly known as “cast iron”, are typically used for extremely hard components such as blades, hot water radiators, industrial casting and lamp post.
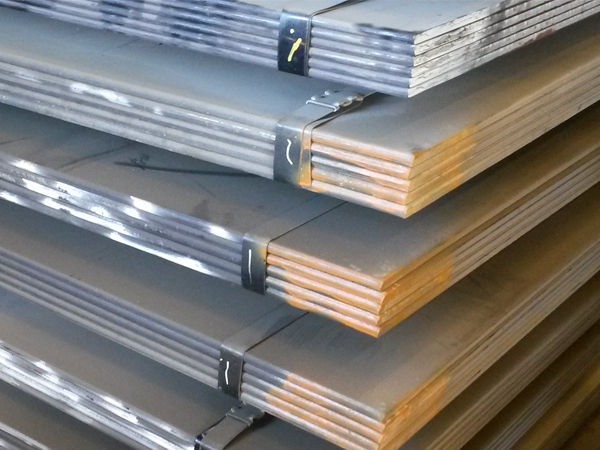

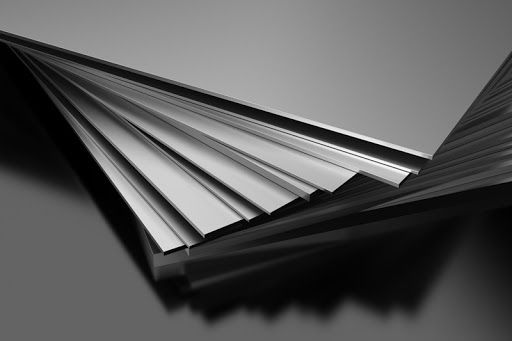

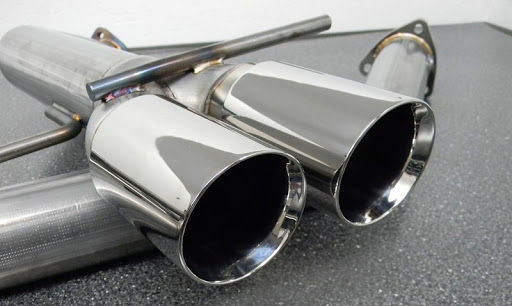

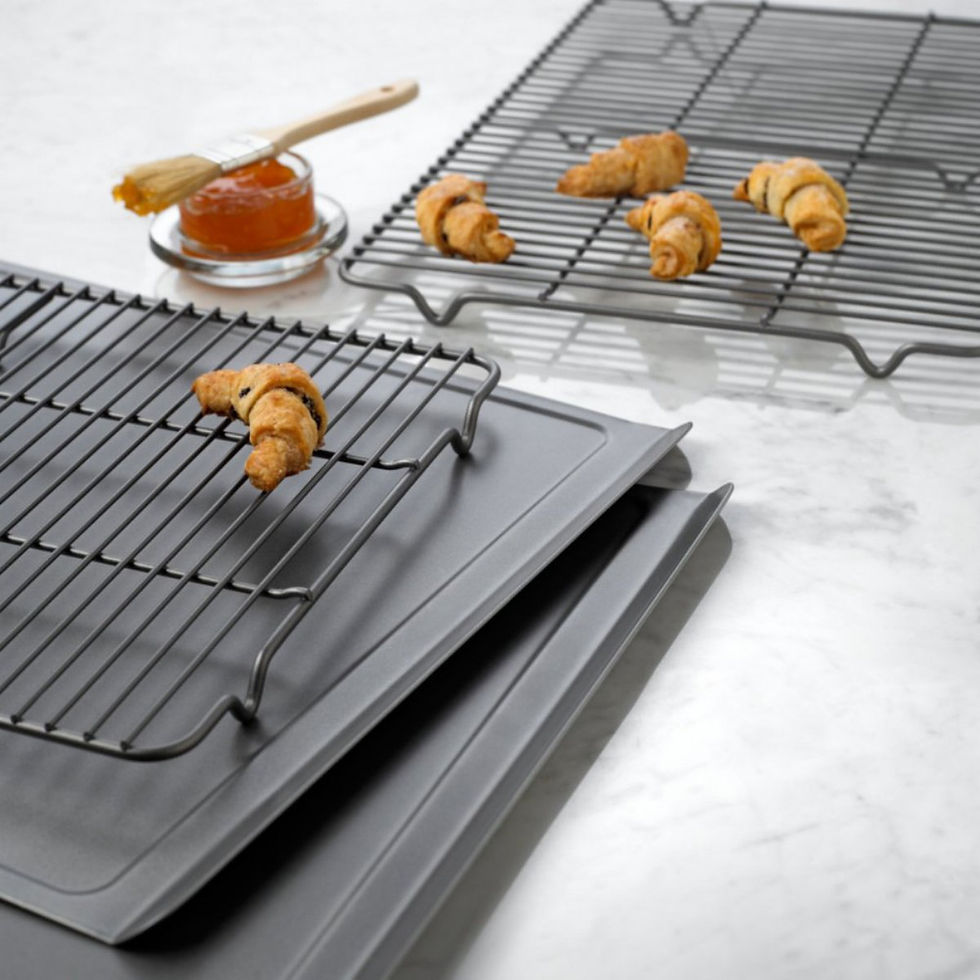
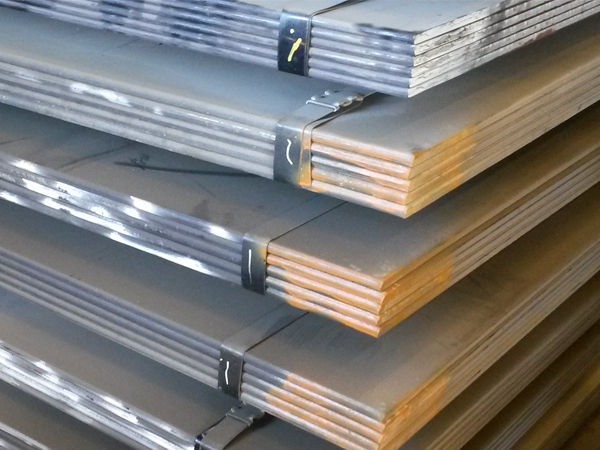

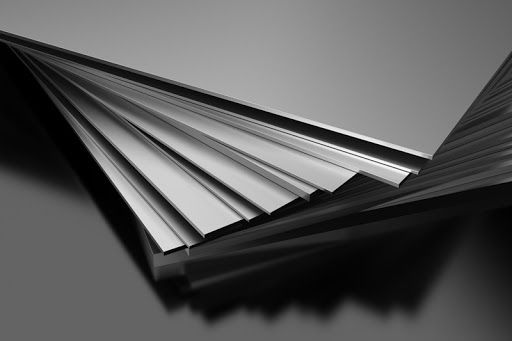

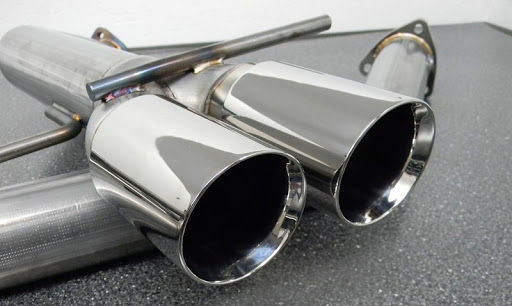

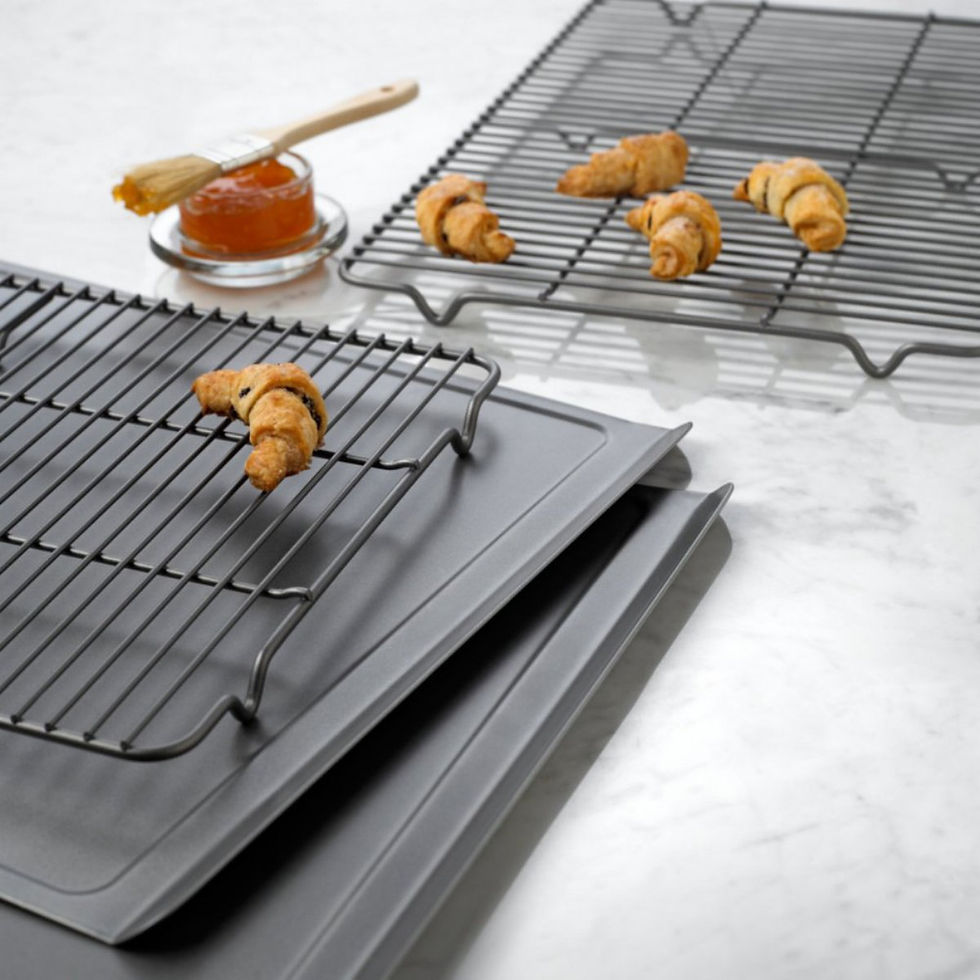
ALUMINIZED STEEL
Both aluminium and steel are considered as the primer of manufacturing materials; while steel is distinguished for its superior strength, aluminium exhibits remarkable resistance to corrosion. Aluminized steel is a sub-division of carbon steel that has been applied with a layer of aluminium-silicon alloy through “hot-dipping”. This process creates a tight bond between the carbon steel base and its alloy coating, forming a compound with advantageous properties, namely, high temperature resistance and low thermal expansion coefficient, which means aluminized steel is less prone to deforming under heat stress. They are therefore ideal for manufacturing incinerators, ovens, heaters, barbeque burners, exhaust systems and mufflers. Its high resistance towards chemicals is also favourable for sanitary applications such as cooking wares and kitchen appliances; and also great for the fabrication of HVAC components and industrial pipes, carrying corrosive liquids. In general, aluminized steel can be divided into two classifications; type 1 which has a coating of 5% to 11% silicon which is typically used for cooking and heating equipment. Type 2, on the other hand, has pure aluminium coating and is used for cladding and jacketing over insulation.
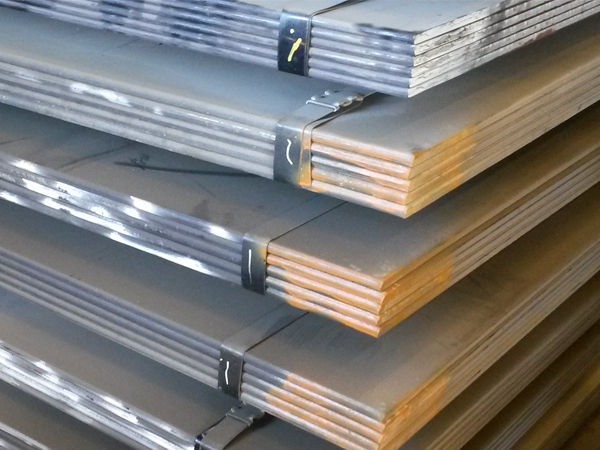

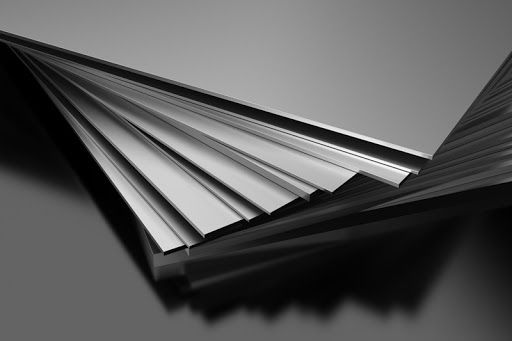

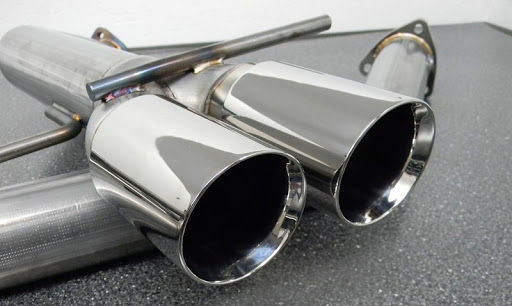

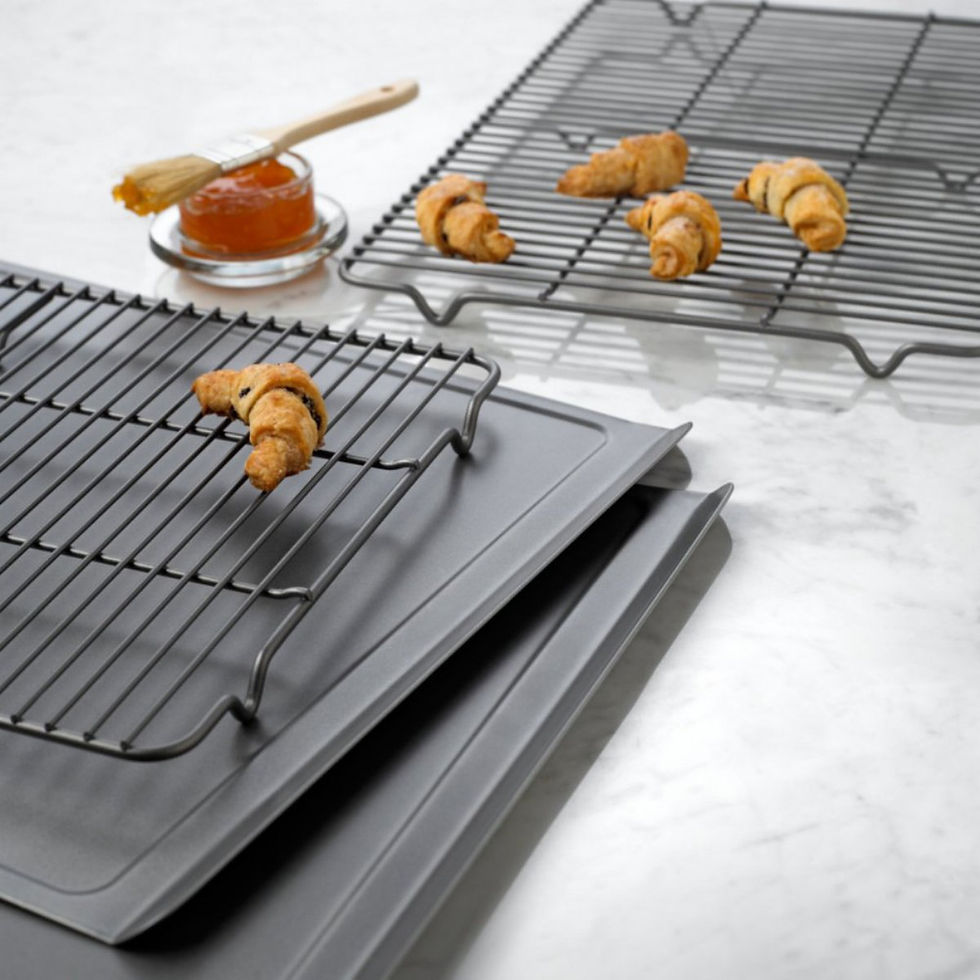
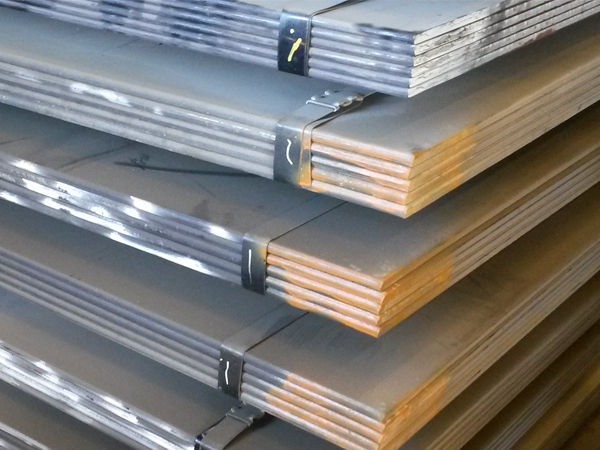

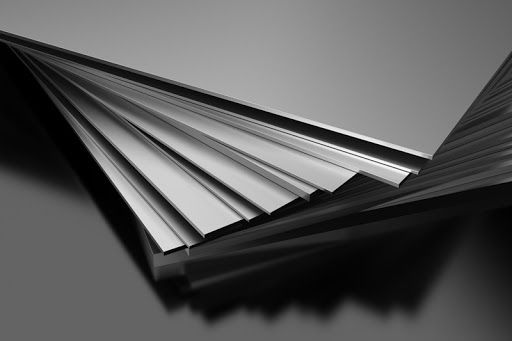

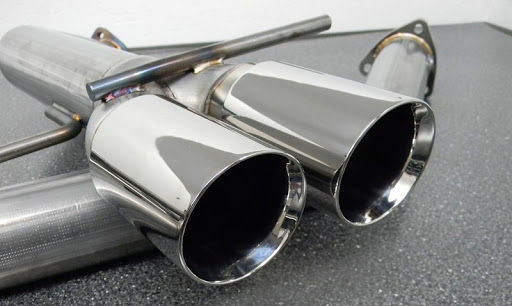

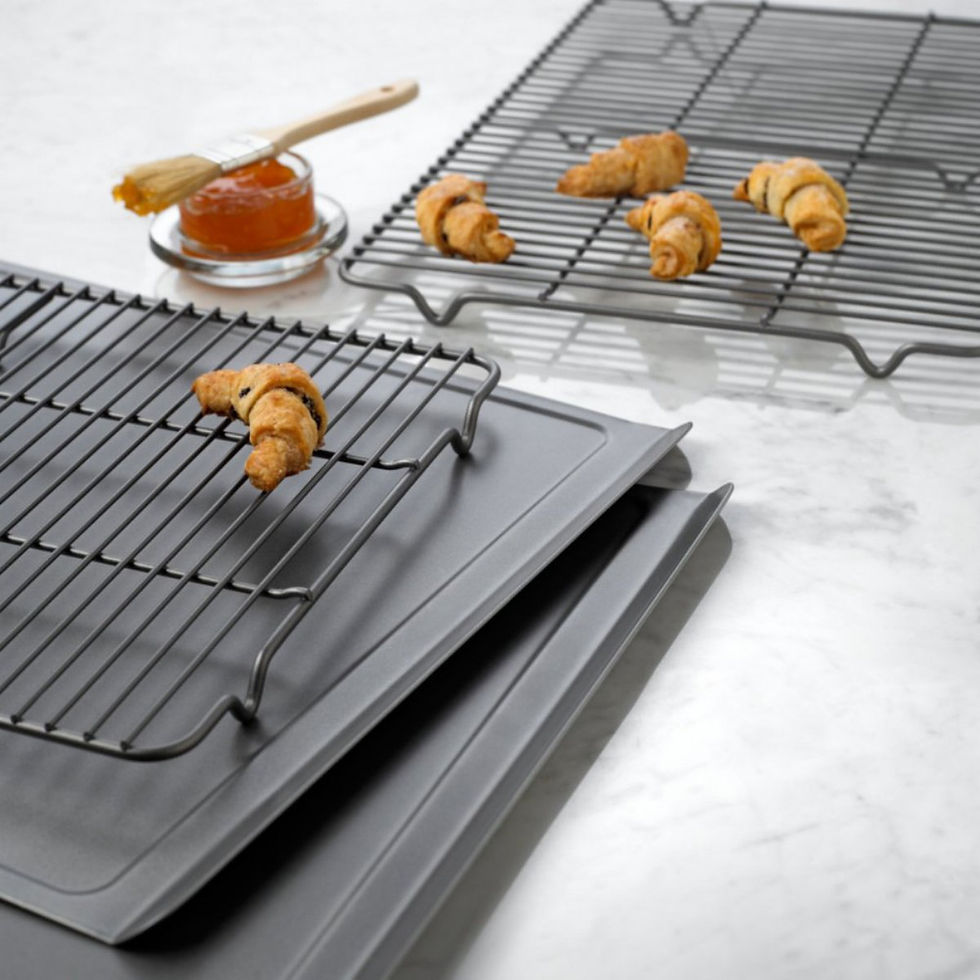
ALUMINIZED STEEL
Both aluminium and steel are considered as the primer of manufacturing materials; while steel is distinguished for its superior strength, aluminium exhibits remarkable resistance to corrosion. Aluminized steel is a sub-division of carbon steel that has been applied with a layer of aluminium-silicon alloy through “hot-dipping”. This process creates a tight bond between the carbon steel base and its alloy coating, forming a compound with advantageous properties, namely, high temperature resistance and low thermal expansion coefficient, which means aluminized steel is less prone to deforming under heat stress. They are therefore ideal for manufacturing incinerators, ovens, heaters, barbeque burners, exhaust systems and mufflers. Its high resistance towards chemicals is also favourable for sanitary applications such as cooking wares and kitchen appliances; and also great for the fabrication of HVAC components and industrial pipes, carrying corrosive liquids. In general, aluminized steel can be divided into two classifications; type 1 which has a coating of 5% to 11% silicon which is typically used for cooking and heating equipment. Type 2, on the other hand, has pure aluminium coating and is used for cladding and jacketing over insulation.

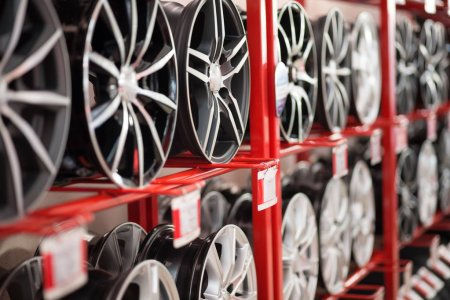



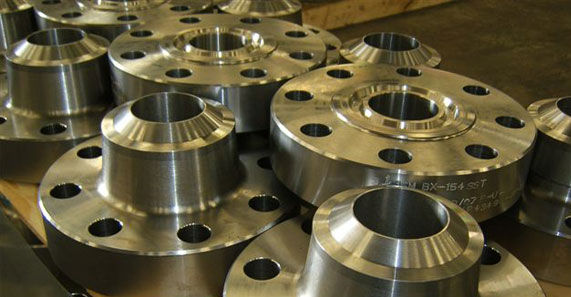
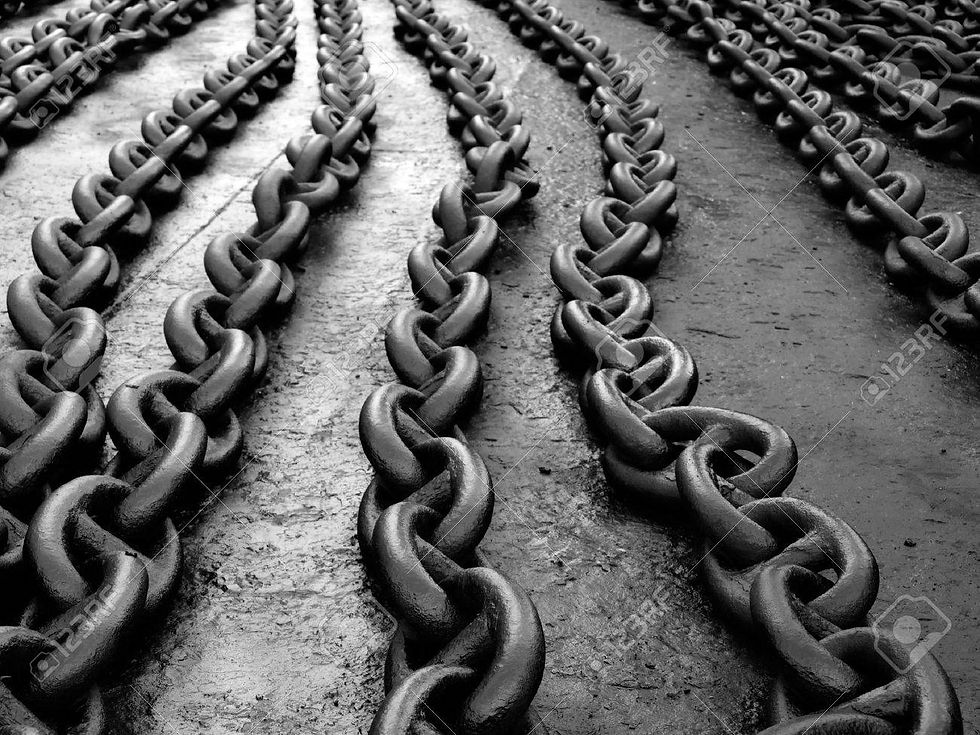

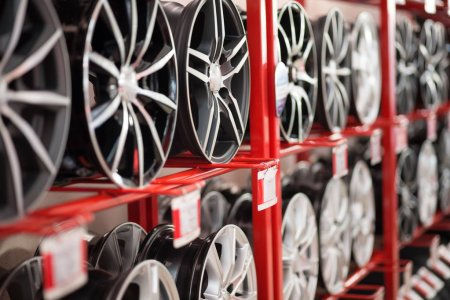



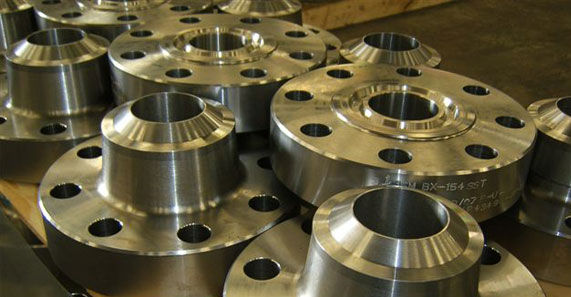
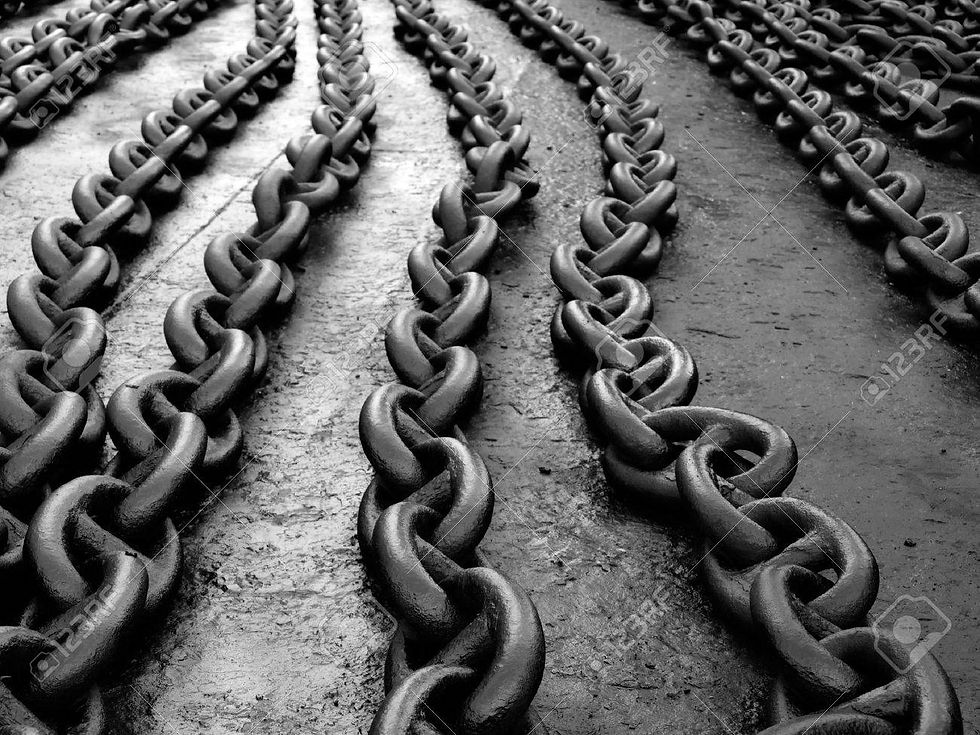
ALLOY STEEL
By definition, steels that contain specified or excessed amounts of foreign elements, other than carbon are in fact known as alloyed steels. Having that said, the term alloy steel, in particular, is reserved for steels that contain only a modest amount of alloying elements and also depends on its thermal treatment. By adding alloying elements, such as manganese, silicon, nickel, titanium, copper, chromium and aluminium, the chemical composition of regular carbon steel is altered and its characteristics can be modified to achieve increased hardness, corrosion resistance, strength and improved ductility. Alloy steels can be divided into a few different grades, which are “through-hardening”, “carburizing” and other specialty grades. Through-hardening grades are heat treated by quenching and tempering, primarily for parts that demand maximum toughness and strength; while carburizing grades, on the other hand, are used when a tough core and considerably shallow, hard surface is needed. They are used for parts that have to withstand wear and high-stresses. As alloy steels are generally more responsive to heat and mechanical treatments, they are widely used in a broad range of industries.

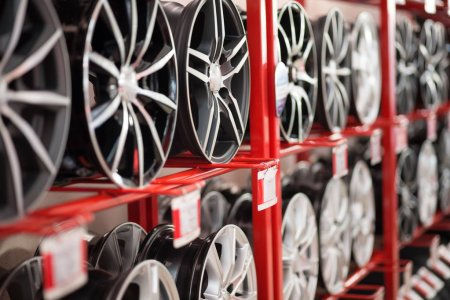



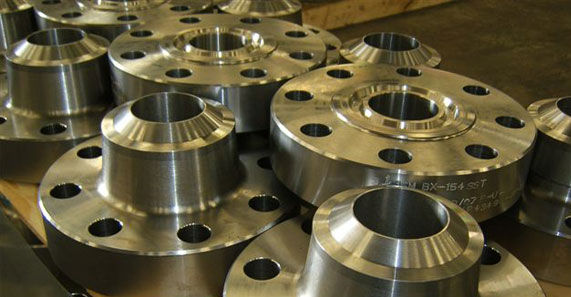
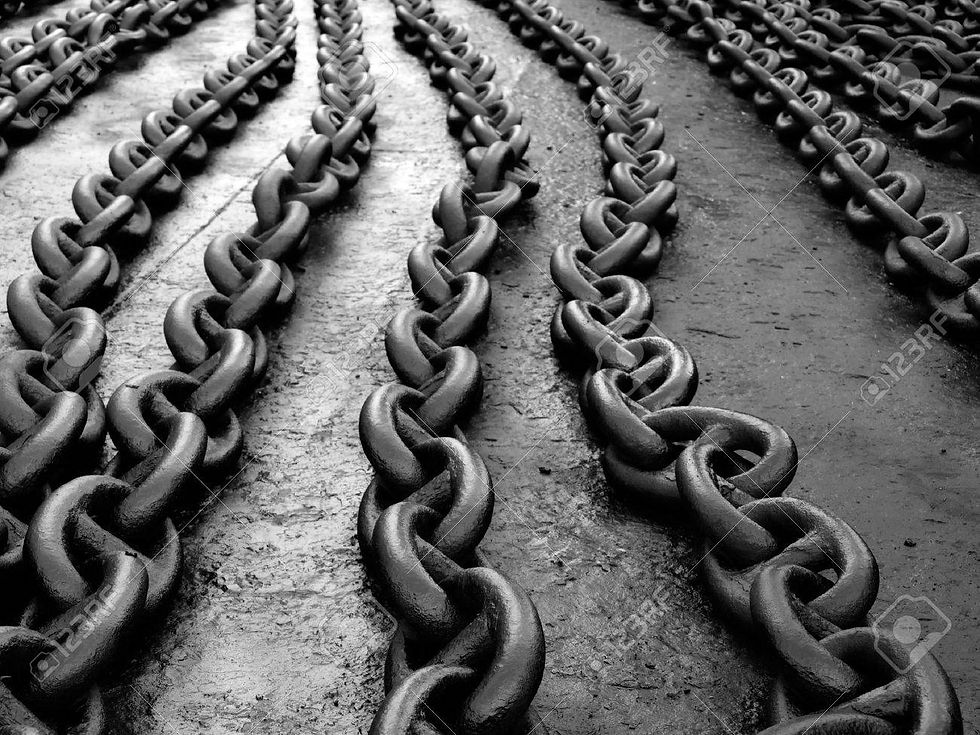

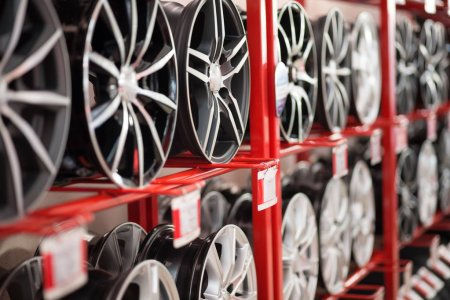



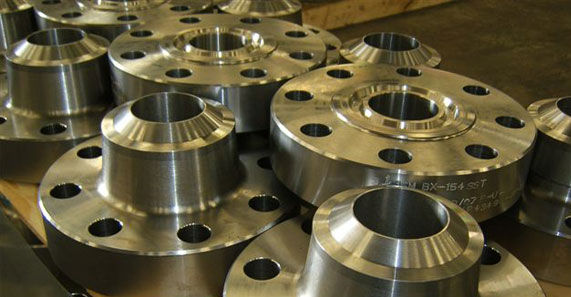
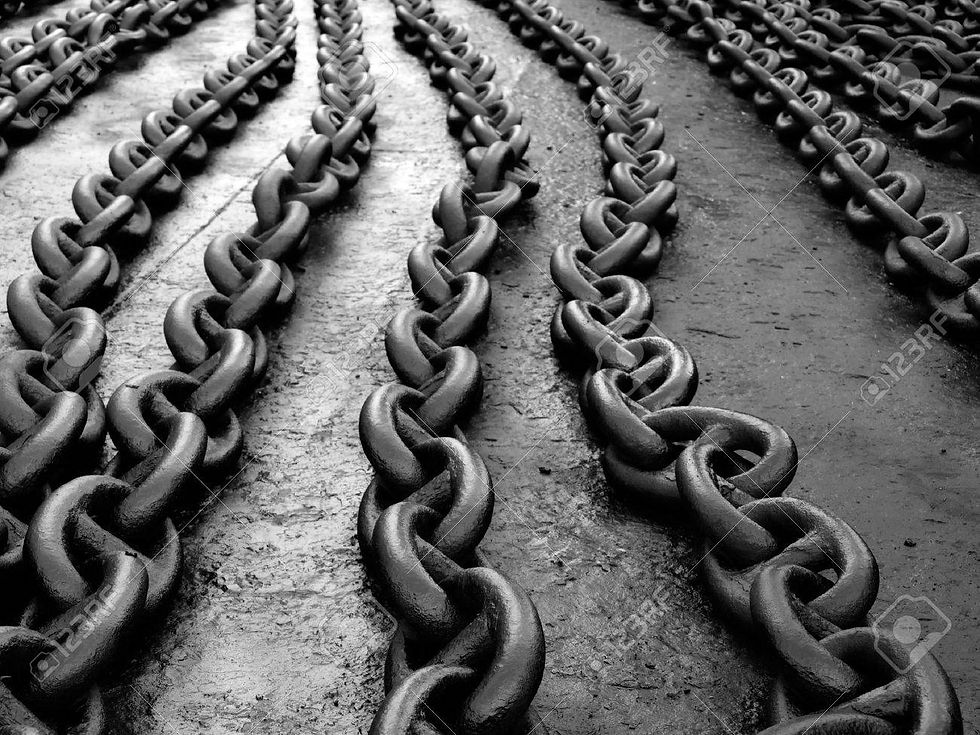
ALLOY STEEL
By definition, steels that contain specified or excessed amounts of foreign elements, other than carbon are in fact known as alloyed steels. Having that said, the term alloy steel, in particular, is reserved for steels that contain only a modest amount of alloying elements and also depends on its thermal treatment. By adding alloying elements, such as manganese, silicon, nickel, titanium, copper, chromium and aluminium, the chemical composition of regular carbon steel is altered and its characteristics can be modified to achieve increased hardness, corrosion resistance, strength and improved ductility. Alloy steels can be divided into a few different grades, which are “through-hardening”, “carburizing” and other specialty grades. Through-hardening grades are heat treated by quenching and tempering, primarily for parts that demand maximum toughness and strength; while carburizing grades, on the other hand, are used when a tough core and considerably shallow, hard surface is needed. They are used for parts that have to withstand wear and high-stresses. As alloy steels are generally more responsive to heat and mechanical treatments, they are widely used in a broad range of industries.
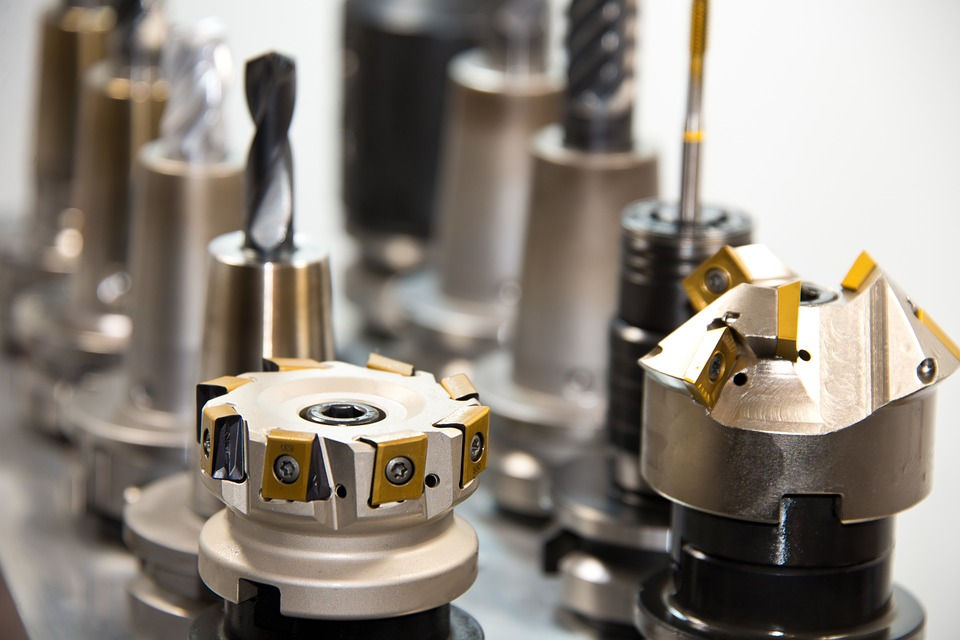
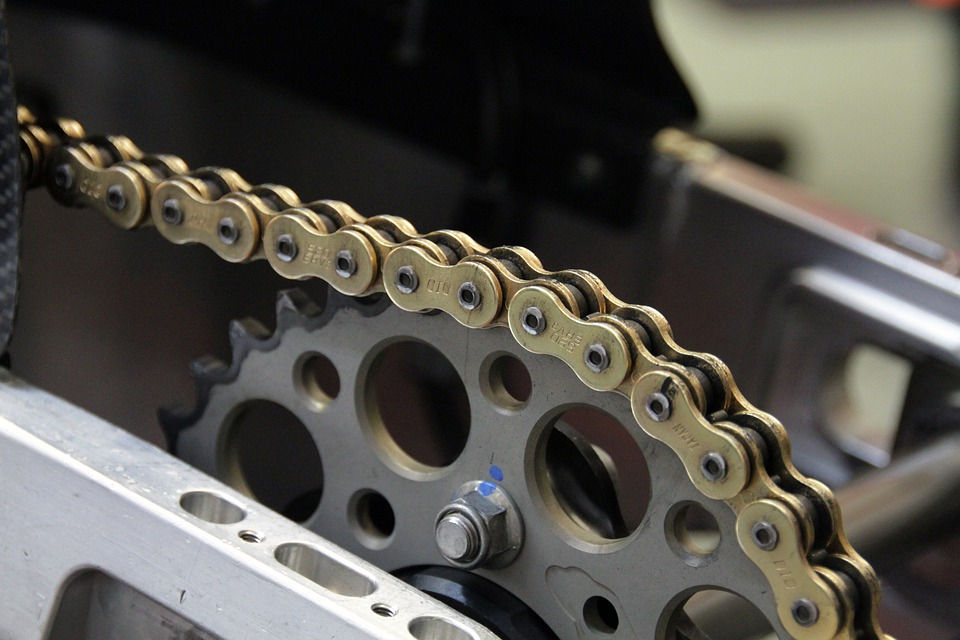


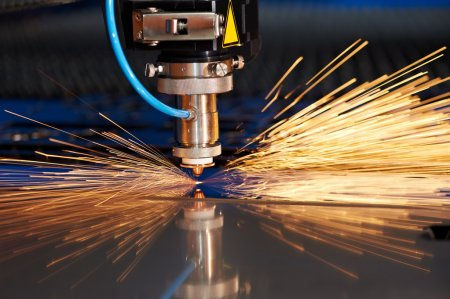
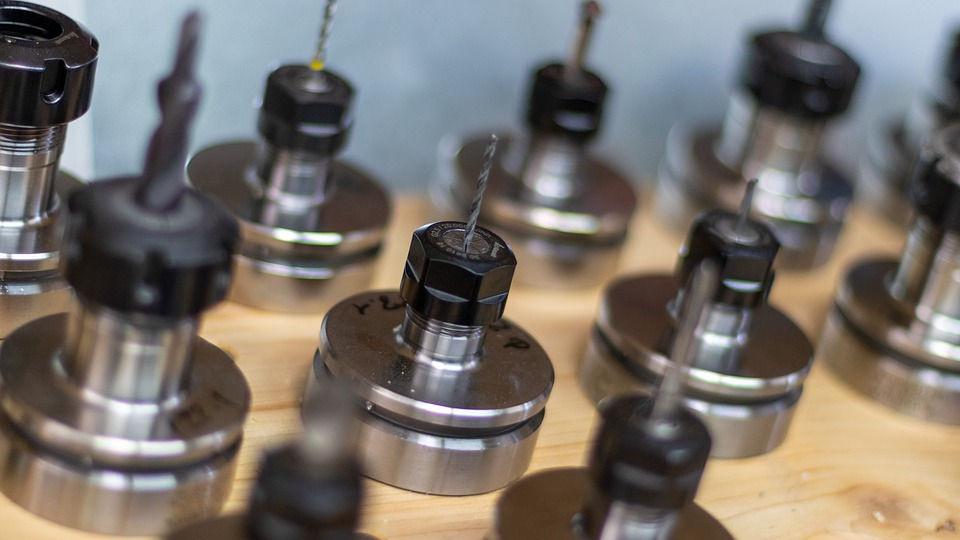


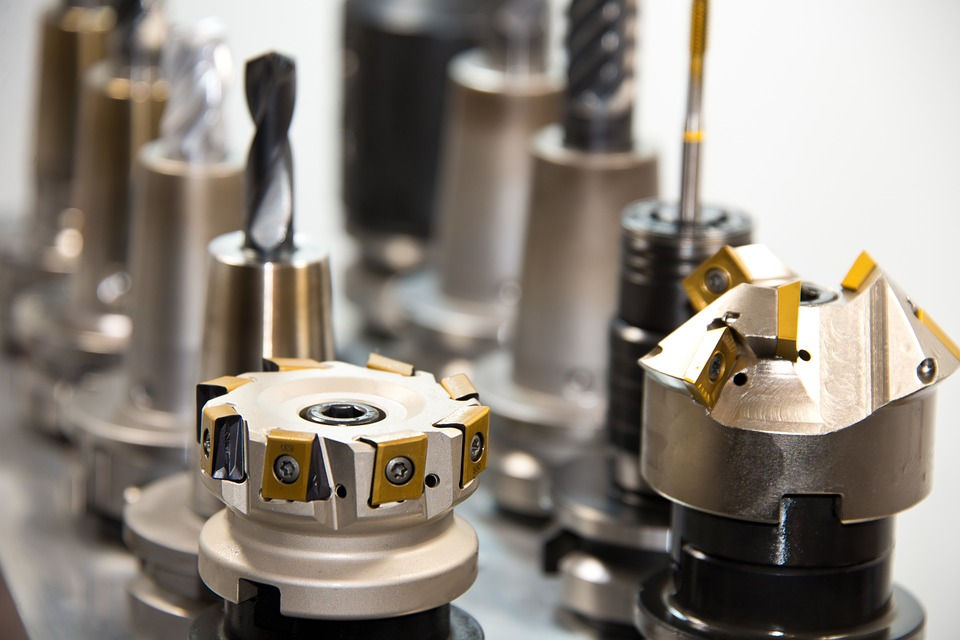
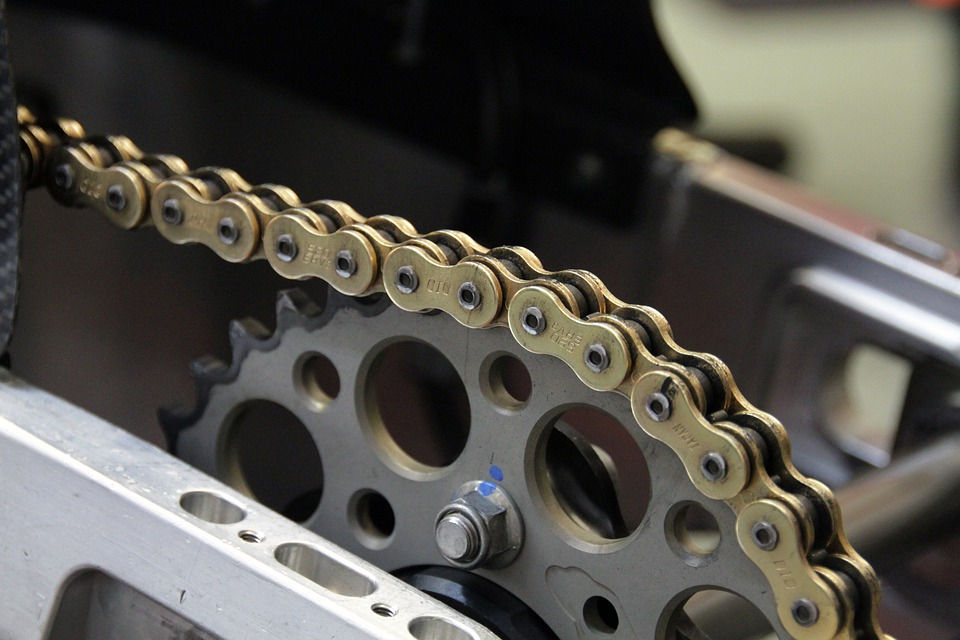


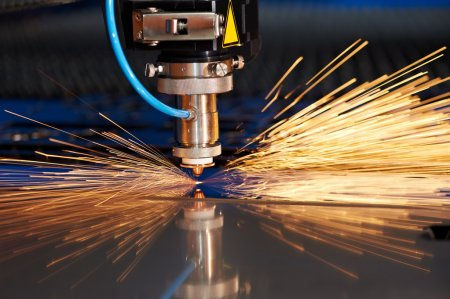
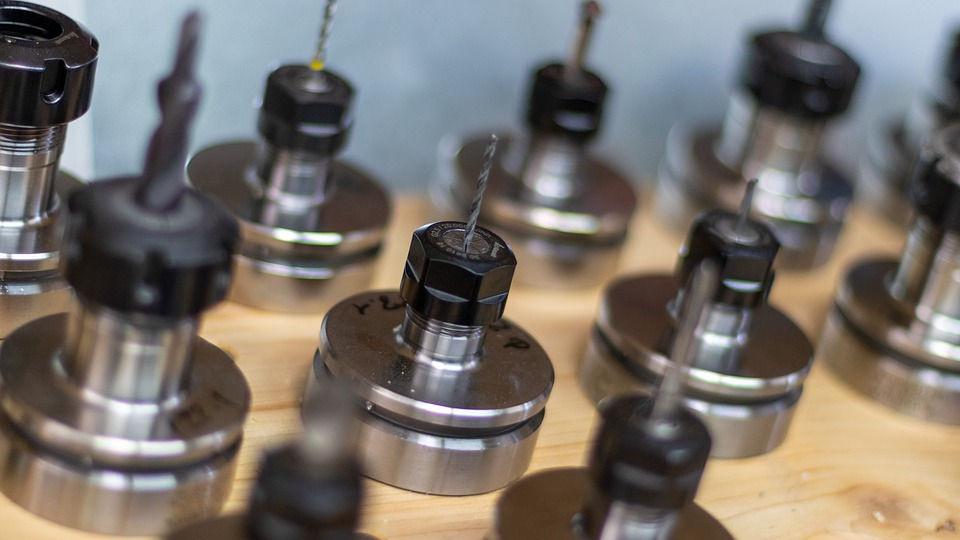


TOOL STEEL
Tool steel is a type of high-carbon alloy steel with a carbon content between 0.5% to 1.5% and contains expensive additives such as tungsten, chromium, vanadium, and molybdenum. As its name suggests, they are intended for tool manufacturing by way of forming cutting, stamping, forming and shaping tools or machine-dies. Tool steels are known for their exceptional hardness, resistance to abrasion and corrosion, and its ability to retain shape at elevated temperatures. These key properties make tool steel ideally suited for critical high-strength applications that require sharp cutting, withstanding impact loading, or when heat treating is required. Generally, tool steels can be categorised into different grades, including, water hardening, air hardening, cold working, oil hardening, shock resistance types and hot working. The choice of grades depend on many factors as according to its industrial applications, for example, hot-work tool steels are used extensively to cut material at high temperatures; oil hardening, on the other hand, is used for cold trimming, arbours, drill bushing and knurling tools; while water-hardening tool steels are generally lower cost and more brittle than other types, and can be used for cutting tools, embossing, and cutleries.
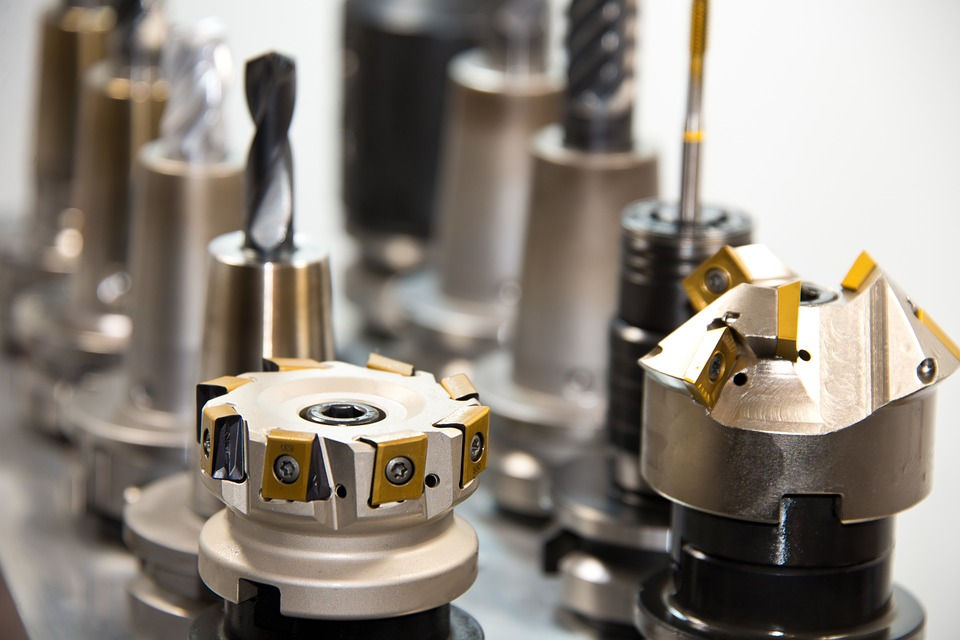
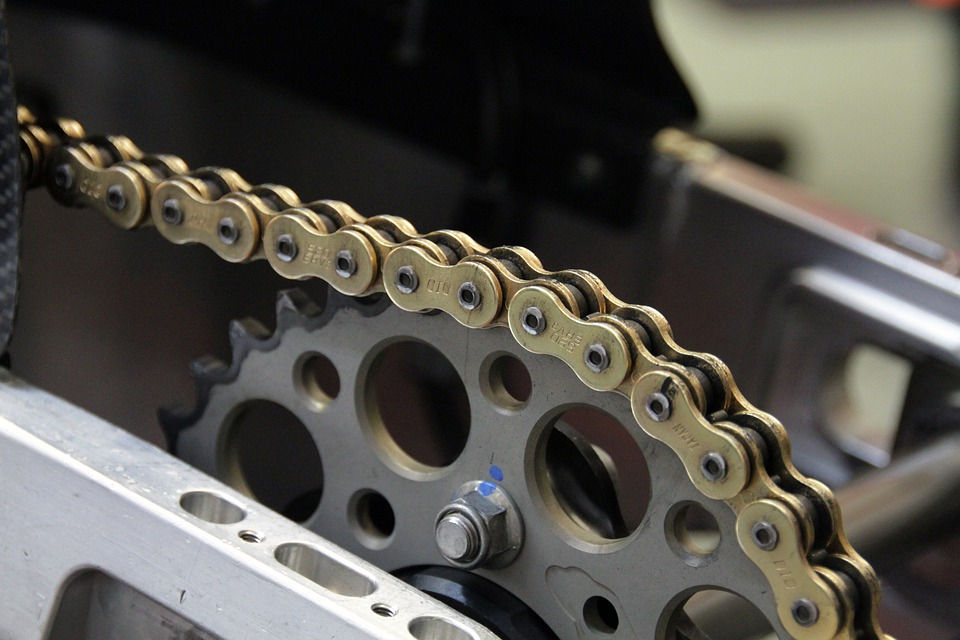


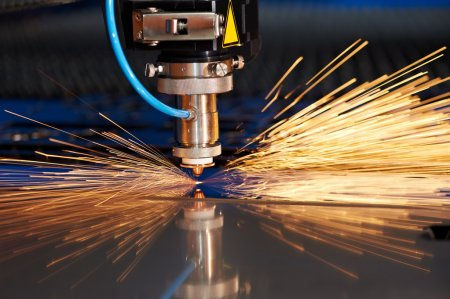
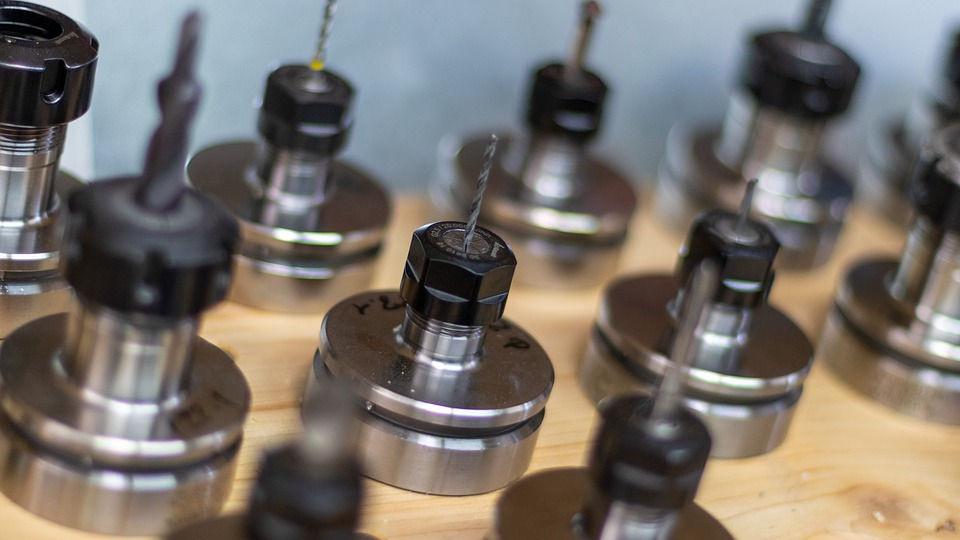


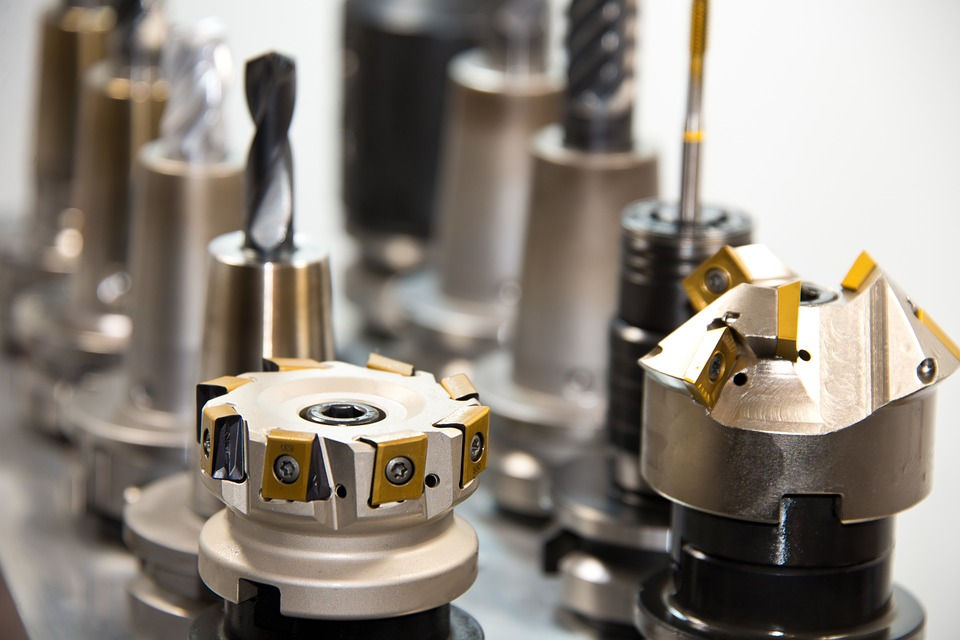
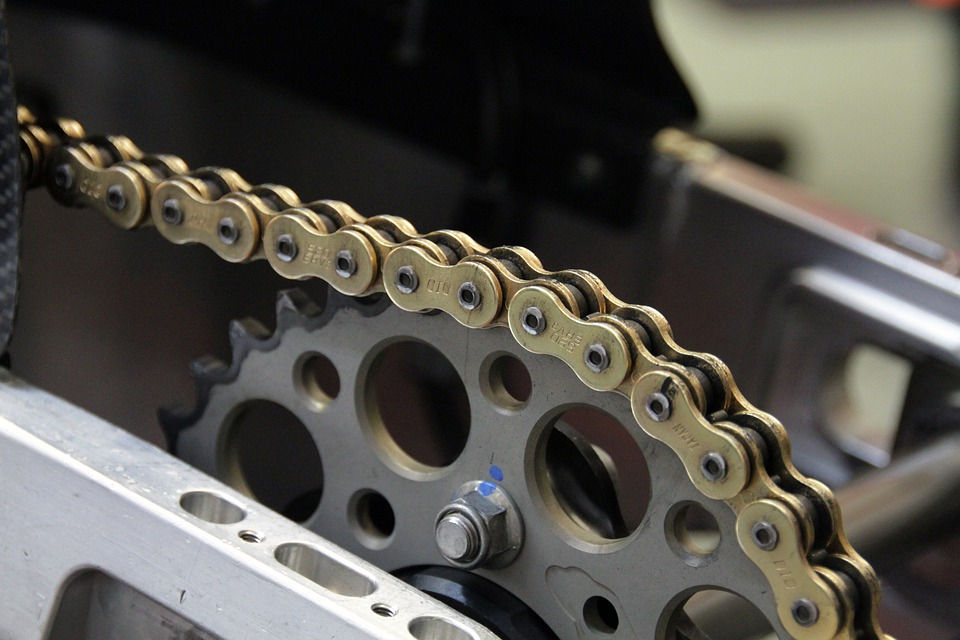


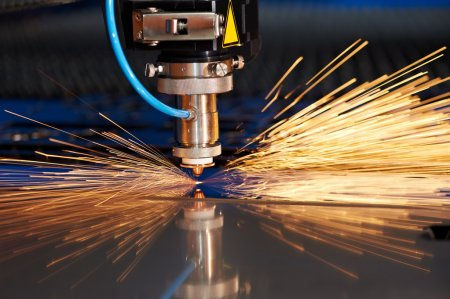
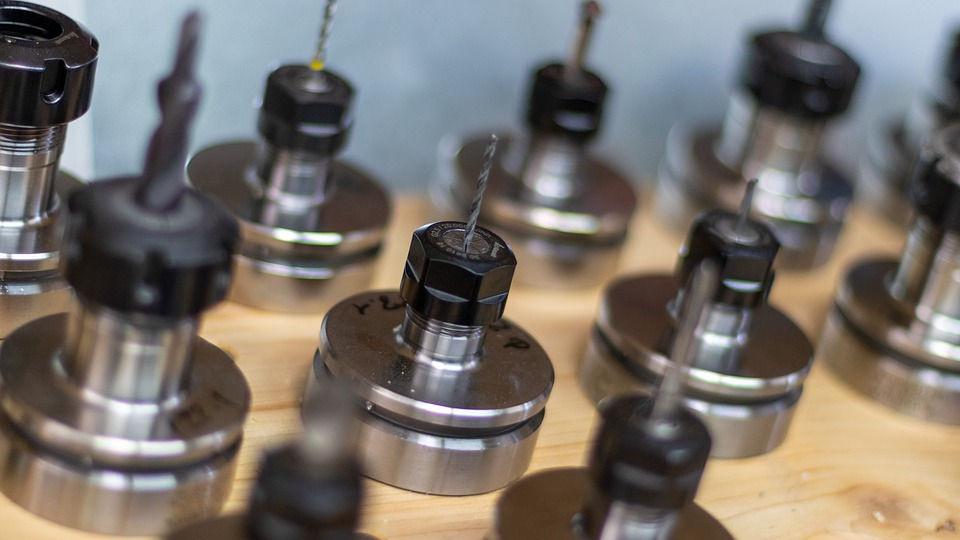


TOOL STEEL
Tool steel is a type of high-carbon alloy steel with a carbon content between 0.5% to 1.5% and contains expensive additives such as tungsten, chromium, vanadium, and molybdenum. As its name suggests, they are intended for tool manufacturing by way of forming cutting, stamping, forming and shaping tools or machine-dies. Tool steels are known for their exceptional hardness, resistance to abrasion and corrosion, and its ability to retain shape at elevated temperatures. These key properties make tool steel ideally suited for critical high-strength applications that require sharp cutting, withstanding impact loading, or when heat treating is required. Generally, tool steels can be categorised into different grades, including, water hardening, air hardening, cold working, oil hardening, shock resistance types and hot working. The choice of grades depend on many factors as according to its industrial applications, for example, hot-work tool steels are used extensively to cut material at high temperatures; oil hardening, on the other hand, is used for cold trimming, arbours, drill bushing and knurling tools; while water-hardening tool steels are generally lower cost and more brittle than other types, and can be used for cutting tools, embossing, and cutleries.
Aathaworld Sdn Bhd is a steel supplier and contractor in Malaysia which provides you different grade of steels for commercial, industry and construction works, covering KL Kuala Lumpur, Klang Valley and other states in Malaysia.
​
​
​
Photo Credits: Depositphotos, pixabay, metal supplies, mabelasteelindustriesfactory, jayeshmetalcorporation, reliance foundry, aksystem, cascadiametals, pop screen, hascallsteel, oilandgaspipingincompanies, rextonsteelalleys, 4130pipefittings, ferocom, 123rf, smartmetalgroup